Fabricated Metal Products
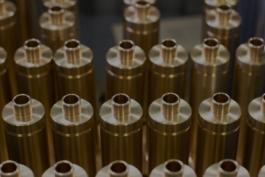
Customer & Market Due Diligence Of Global Precision Parts Manufacturer: Validating Revenue Sustainability In Markets Under Transformational Changes
Conducted a 2-week customer & market due diligence to validate the sustainability and growth outlook of target’s key product application/programs. To this end, Gotham: built a model to establish impact of automotive electrification on target’s business; analyzed target’s top product applications/ programs to establish growth outlook, program lifecycle, target’s positioning, and margin outlook; conducted anonymous and “warm introduction” interviews with target’s customers; reconciled target’s financial projections against market forecast to determine how much of target’s projected growth was coming from market share gains; and established competitive landscape for both mechanical and electric parts. Gotham’s work established that target’s business was sustainable and gave our client confidence to proceed with its investment.
Show Details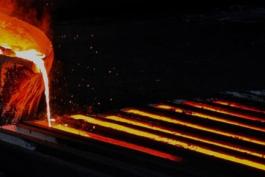
Operational Due Diligence of Fabricated Metal Products Holding Company: Properly Valuing Diverse Manufacturing Operations
Analyzed operations and cost structure of 5 independent companies engaged in forging, casting, and stamping operations. Deciphered cost structure, reviewed manufacturing operations, and analyzed material spend. Identified $7-15MM of labor, overhead, and material cost reduction opportunities in the largest of the companies, which was engaged in steel casting. Identified another $6-9MM in scheduling, labor, efficiency, and consolidation opportunities for the remaining companies. After delayed acquisition, now helping to capture opportunities.
Show Details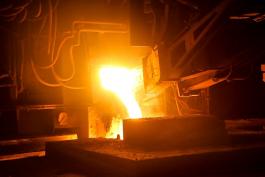
Material Cost Reduction at Large Steel Castings Manufacturer: Material Purchasing and Usage Reduction
Identified $3.3-5.5MM in material cost reduction opportunities in both purchasing and material usage, including: clawing back commodity price increases; consolidating vendor base and re-sourcing key commodities; measuring and reducing material usage; and tracking and controlling non-centralized discretionary purchases. Developed tools to allow robust, ongoing reporting and analysis capabilities for both purchasing and usage performance and created the bid packages for top 6 commodities to launch the re-sourcing process. Within weeks, client team reduced usage by 3%, generating $1.2MM in savings, and completed several re-sourcing initiatives.
Show Details
Operations Improvements at Leading Industrial Goods Manufacturer: Achieving and Sustainng World-class Performance
Implemented a 2-phased approach to turn around delivery performance - a "Stop The Bleeding" Phase focused on tactical fixes to get situation under control and a "Sustainable World Class Performance" Phase focused on addressing systematic issues to ensure sustainability. Achieved a 40% reduction in delivery backlog and 32% improvement in on-time delivery.
Show Details
Complexity Management for Full-line Industrial Goods Manufacturer: Developing Segmented Operations and Service Strategy
Devised an approach for segmenting SKUs in a diverse SKU environment based on a several qualitative factors such as contractual customer requirements, marketing strategy, and sourcing considerations, and a statistical scoring methodology incorporating several demand pattern factors such as sales, margin, demand variability, demand frequency, broken shipments, and requirements of top customers. Devised and implemented differentiated operations and service strategy (make-to-stock vs. manufacture-to-order) for the SKU segments which contributed to an 28% improvement in on-time delivery and a 25% reduction in inventory.
Show Details
Delivery Performance Turnaround at Leading Industrial Goods Manufacturer: Rapid Reduction In Delivery Backlog
Identified quick tactical solutions to address process issues responsible for delivery backlog. Created a backlog prioritization tool to identify and value component shortages that permitted prioritization of work orders and purchase orders. Achieved backlog reduction by more than two-thirds in short finished goods in 5 months.
Show Details