Fabricated Metal Products
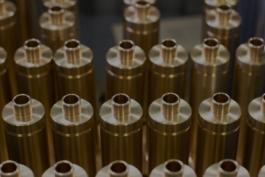
Customer & Market Due Diligence Of Global Precision Parts Manufacturer: Validating Revenue Sustainability In Markets Under Transformational Changes
Conducted a 2-week customer & market due diligence to validate the sustainability and growth outlook of target’s key product application/programs. To this end, Gotham: built a model to establish impact of automotive electrification on target’s business; analyzed target’s top product applications/ programs to establish growth outlook, program lifecycle, target’s positioning, and margin outlook; conducted anonymous and “warm introduction” interviews with target’s customers; reconciled target’s financial projections against market forecast to determine how much of target’s projected growth was coming from market share gains; and established competitive landscape for both mechanical and electric parts. Gotham’s work established that target’s business was sustainable and gave our client confidence to proceed with its investment.
Show Details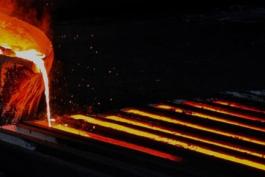
Operational Due Diligence of Fabricated Metal Products Holding Company: Properly Valuing Diverse Manufacturing Operations
Analyzed operations and cost structure of 5 independent companies engaged in forging, casting, and stamping operations. Deciphered cost structure, reviewed manufacturing operations, and analyzed material spend. Identified $7-15MM of labor, overhead, and material cost reduction opportunities in the largest of the companies, which was engaged in steel casting. Identified another $6-9MM in scheduling, labor, efficiency, and consolidation opportunities for the remaining companies. After delayed acquisition, now helping to capture opportunities.
Show Details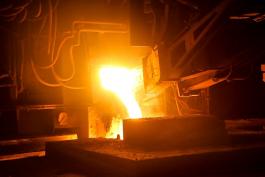
Material Cost Reduction at Large Steel Castings Manufacturer: Material Purchasing and Usage Reduction
Identified $3.3-5.5MM in material cost reduction opportunities in both purchasing and material usage, including: clawing back commodity price increases; consolidating vendor base and re-sourcing key commodities; measuring and reducing material usage; and tracking and controlling non-centralized discretionary purchases. Developed tools to allow robust, ongoing reporting and analysis capabilities for both purchasing and usage performance and created the bid packages for top 6 commodities to launch the re-sourcing process. Within weeks, client team reduced usage by 3%, generating $1.2MM in savings, and completed several re-sourcing initiatives.
Show Details
Post-Merger Integration of South American Industrial Goods Manufacturer: Harvesting Opportunity from Performance, Capability, and Cost Structure Enhancement
Identified specific actionable opportunities (cost, service, and quality) to capitalize on post-merger opportunities. Created plan to capture significant near term and longer term performance, capability, and cost structure enhancements. Management-led execution targeted to result in $2MM in cost, service, and quality savings (on a cost base of $5.5MM).
Show Details
Customer Service and Delivery Issues at Leading Industrial Hardgoods Manufacturer: New Planning/Delivery Capabilities at MachiningCo
Led diagnostic-based effort culminating in enhanced planning and delivery capabilities: short-term tactical prioritization to overcome to overcome significant backlog; new planning system parameters; customer-oriented delivery strategy, including fast-ship program; shop-floor prioritization mechanisms (fixed schedule); measurement/tracking and reporting scheme for planning and production; ultimate migration to integrated MRP system. Fast- ship SKU program reduced order-to-delivery cycle from 2+ weeks to 1 day; $10MM backlog reduced to $2.5MM (including future orders) within 3 months.
Show Details
Manufacturing Strategy at Leading Industrial Hardgoods Manufacturer: Creating Sustainable Cost Improvements
Worked with manufacturing management to re-evaluate the existing manufacturing strategy taking into consideration all sourcing options (e.g. automation in U.S. plants, outsourcing, relocation). Profiled U.S. manufacturing operations by product and process type, and performed comparable profile of selected sited in Mexico and Asia, as well as developed economic profiles for outsourcing options and a business case for automation opportunities. Recommended strategy included moving high-volume assembly to Mexico, consolidating low-volume assembly in a single U.S. plant, selected automation, and outsourcing of non-core operations. Based on execution of our plan, company: captured $9MM in labor savings, eliminated $2MM in overhead, and avoided $6-7MM in capital expense.
Show Details