Production Planning & Scheduling
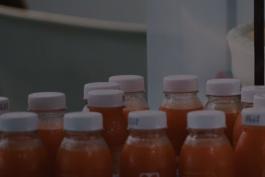
Network-wide Operating System to Turn Around Performance at Foodservice/Co-pack Juice Company
Turned around plant performance by implementing basic plant operating system (downtime, waste, and scheduling). $600K in run rate cost savings captured by the end of the 6-week engagement, with tools and processes in place to capture the rest. Building on the initial success, rolled out the network-wide standard operating procedures to the other 2 plants during an 8-week Phase II effort with additional savings of $2-2.5MM expected. Company generating record EBITDA (60+% improvement in EBITDA) and the PE firm decided to market the company for an exit.
Show Details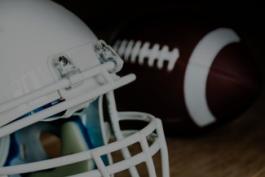
Enhancing Forecasting, Planning, and Product Lifecycle Management in Post-merger Environment at Leading Sporting Safety Equipment Company
Assisted 4 client teams and trained client personnel during a post-merger replenishment system enhancement and inventory reduction effort. Developed a centralized inventory and planning model by merging information from 2 separate operating entities. Achieved $8+MM reduction in inventory in 9 months.
Show Details
New Planning/Delivery Capabilities to Turnaround Customer Service/Delivery Performance at Leading Industrial Hardgoods Manufacturer
Led diagnostic-based effort culminating in enhanced planning and delivery capabilities: short-term tactical prioritization to overcome to overcome significant backlog; new planning system parameters; customer-oriented delivery strategy, including fast-ship program; shop-floor prioritization mechanisms (fixed schedule); measurement/tracking and reporting scheme for planning and production; ultimate migration to integrated MRP system. Fast- ship SKU program reduced order-to-delivery cycle from 2+ weeks to 1 day; $10MM backlog reduced to $2.5MM (including future orders) within 3 months.
Show Details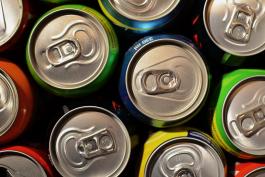
Throughput and Cost Improvements to Become a Competitive Full-line Beverage Co-packer
2 week diagnostic that benchmarked conversion costs for the company and identified 15-20% in cost reduction opportunities. The effort indicated that with improved scheduling processes and more efficient use of labor, the company could save at least $1.5MM in the short-term. Recommendations also included putting in place a system to track true costs and performance to enable longer-term improvements.
Show Details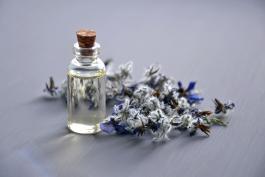
Uncovering Cost and Inventory Savings Opportunities and Assessing Operational Capabilities at Licensed Brands Household Goods Company
Conducted 1-week opportunity assessment for inventory, labor, material, freight, distribution, and overhead costs from both standalone and synergistic perspective. Identified $3-4MM in cost reduction opportunities and $4-5MM in inventory reduction opportunities. Client acquired the company and merged it with a portfolio consumer goods company. Subsequently, assisted in capturing $4-5MM in inventory and $2MM in freight savings at this growing company which became one of the largest suppliers to big box retailers.
Show Details
Cleaning Up Distribution as a First Step in Establishing a Growth-supporting Distribution Platform at National Seafood Company
Conducted a diagnostic to reduce distribution costs as a part of an effort to integrate the distribution systems of two companies by identifying and sizing cost levers with savings benefits (quick hits, process changes, and cultural changes). Targeted cost savings of $1.5 to 2MM on a base of $7MM, of which $1MM are estimated to be achieved by quick hits alone.
Show Details