Make Vs. Buy
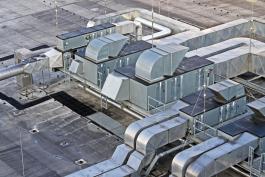
Establishing Operation End-vision for a Fast-growing, Entrepreneurial Climate Control Product Manufacturer
Conducted a 3-week operations diagnostic to establish an end-vision for optimizing the clients’s manufacturing, supply chain, and engineering operations. Gotham developed a solid fact base of the client’s operations, including demand patterns, inventory, labor efficiency, product complexity, and cost structure. Working with management, Gotham created an end-vision to transform operations and generate both real bottom line benefits – 600bp EBITDA improvement, 20-30% reduction in inventory, and 30% reduction in the plant footprint – and capability enhancements (faster speed to market, improved quality, etc.) that will allow the client to capture market opportunities and drive future growth. The company’s board wholeheartedly backed this end-vision and asked Gotham to help accelerate capture of these opportunities.
Show Details
Outsourcing Non-core Operations to Improve EBITDA, Avoid CapEx, and Reduce Operational Complexity at Specialty Industrial Equipment Manufacturer
Identified potential for outsourcing non-core activities, created phased plan, and helped with phase 1 (PC board assembly). Prepared client teams to handle subsequent outsourcing targets. Annual conversion and material cost savings ranging from 6% (transformers) to 20% (stuffed PCBs), with $4.5MM in near-term capital avoidance.
Show Details
Rapidly Establishing Manufacturing Outsourcing Economics And Requirements At Family-owned Food, Personal, And Home Care Products Manufacturer
Conducted rapid operational due diligence to establish manufacturing outsourcing economics at a family-owned food, personal care, and home care products manufacturer. Gotham quickly: built a bottom-up view of the target’s cost structure, current product costs, co-pack costs, and organization structure; conducted plant walkthrough and interviewed operations management; and interviewed companies in food and personal care products outsourcing. We established that outsourcing economics are slightly favorable as logistics and G&A would generate sufficient savings to more than offset a slight increase in food manufacturing cost. As our assessment indicated higher costs and risks associated with outsourcing food products, our client successfully pursued a restructured transaction of carving out personal and home care brands and products.
Show Details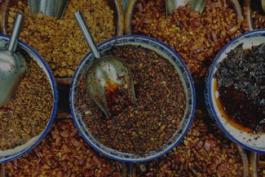
Assessing Operational Scalability to Support Targeted Growth at Family-owned Branded Ethnic Foods Manufacturer
Built operational performance fact base and cost model for due diligence of an entrepreneurial company. Effort included: first-hand observation of operations, management interviews, data collection and synthesis, equipment condition and capex requirement assessment, food safety review, and interviews with potential co-packers. Established that: the existing plant can meet the buyer's target of growing the business 2-3X current volume; identified 5-6 viable and interested co-packers; identified opportunities to reduce cost per case by 16-17.5%; and provided a road map for improving operations. The PE firm is in process of closing the deal.
Show Details
Finding and Valuing Cost Reduction Opportunities at Global Tier 2 Automotive Components Supplier
Conducted opportunity assessment at Tier 2 Automotive Parts supplier with manufacturing locations in 4 countries. Identified $6-9MM in short-term and $27-37MM in longer-term cost reduction opportunities. Near-term opportunities included improving efficiency of US operations and re-sourcing materials and components from lower cost locations. Longer-term opportunities involved closing a European facility, migrating labor-intensive products from the US to Mexico facility, and building up a Chinese JV to supply all Asia product needs. Identified opportunities far exceeded management plan.
Show Details
Harvesting Opportunity from Performance, Capability, and Cost Structure Enhancement at South American Industrial Goods Manufacturer
Identified specific actionable opportunities (cost, service, and quality) to capitalize on post-merger opportunities. Created plan to capture significant near term and longer term performance, capability, and cost structure enhancements. Management-led execution targeted to result in $2MM in cost, service, and quality savings (on a cost base of $5.5MM).
Show Details