Supply Chain Strategy/ Roadmap

Rapid Inventory and Supply Chain Cost Structure Diagnostic at Niche Apparel Producer
Conducted an inventory and cost structure diagnostic and created a plan for capture of opportunities at a recently acquired private equity portfolio company. Identified $11+MM in inventory reduction, $1.2–1.9+MM in overhead expense reduction, and $0.4–1.2MM in freight cost reduction opportunities.
Show Details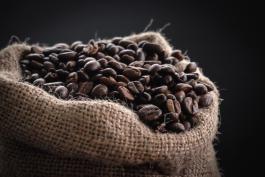
Identifying Consolidation Opportunities and Creating Roadmap for Professionalizing Operations to Support Future Growth at Regional Family-owned Coffee Roaster and Distributor
Conducted a 3-week operational due diligence to establish a robust fact base of cost and operational performance in a data-poor situation, identify consolidation opportunities, and provide a fact-based, actionable plan for post-acquisition value creation, including: delivery and service route optimization to eliminate 30-40% of current routes; brewing equipment CapEx reduction through better deployment of used equipment; warehouse consolidation; sourcing efficiencies; SKU complexity management and inventory reduction; and professionalization of roasting and supply chain operations. Gotham’s findings enabled the client to close the transaction with confidence; the company started capturing identified opportunities within a few weeks of the deal closure.
Show Details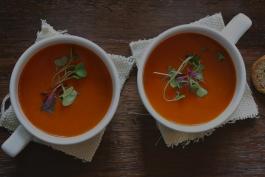
Refocusing North American Supply Chain for a New Competitive Environment at Global Soup Manufacturer
Created a North American Supply Chain strategy for a multinational soup company which had lost its scale advantages. Built upon a solid understanding of the company's operating strengths, the strategy leveraged collaborative alliances up and down the supply chain to extend the company's control of cans from fabrication to retail, and reduce costs in the entire system by 10-15%.
Show Details
Helping Synthesize North American Supply Chain Capabilities into an Optimized System at Global Packaged Food Manufacturer
Led study to create a North American manufacturing strategy that minimized total delivered cost, optimized the asset base, provided for future product needs, and enabled superior customer service. Structured and conducted rigorous analysis to establish comprehensive understanding of current performance within the multiple-plant network. Study results included identification of $24-46 million cost improvement opportunity and the redesign of company's capital allocation process.
Show Details