Labor Productivity

Rapidly Capturing Manufacturing And Logistics Cost Reduction Opportunities At Ethnic Foodservice Products Manufacturer
Captured $1.2MM in operations run-rate savings in 12 weeks at an ethnic foodservice and retail private label products manufacturer by implementing shop floor management best practices. Gotham worked on the shop floor to: observe operations; identify potential improvement opportunities; provide immediate guidance to client personnel; and troubleshoot and pilot solutions. We improved line through from ~225 cases/shift to ~375 cases/shift, reduced fill weight by 3-7% to minimize overfill, reduce floor scrap by 50%; and eliminated expired rework scrap. To ensure sustainability and further improvements, we: trained client personnel, put in place process changes, tools, KPIs and reporting system; and identified/planned next set of improvement opportunities. Gotham also launched logistics savings capture by developing direct ship pilot and facilitating conversation between company sales teams and foodservice distributors.
Show Details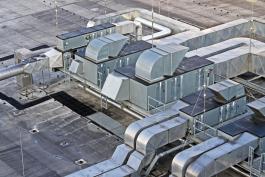
Establishing Operation End-vision for a Fast-growing, Entrepreneurial Climate Control Product Manufacturer
Conducted a 3-week operations diagnostic to establish an end-vision for optimizing the clients’s manufacturing, supply chain, and engineering operations. Gotham developed a solid fact base of the client’s operations, including demand patterns, inventory, labor efficiency, product complexity, and cost structure. Working with management, Gotham created an end-vision to transform operations and generate both real bottom line benefits – 600bp EBITDA improvement, 20-30% reduction in inventory, and 30% reduction in the plant footprint – and capability enhancements (faster speed to market, improved quality, etc.) that will allow the client to capture market opportunities and drive future growth. The company’s board wholeheartedly backed this end-vision and asked Gotham to help accelerate capture of these opportunities.
Show Details
Focusing and Accelerating Labor and Freight Cost Reductions at Branded Consumer Goods Company
Identified and help capture immediate cost savings opportunities in a recently acquired portfolio company that fell short on EBITDA target and violated bank covenants. Effort included 3-4 week development of $1-2MM cost reduction plan and 6-week assistance in capturing $900K labor and outbound freight opportunities, accounting for 15% increase in EBITDA.
Show Details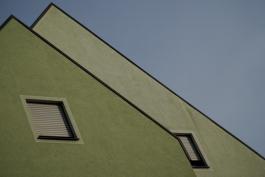
Assessing Manufacturing Capabilities and Scalability to Support Aggressive Growth Projections at Startup Green Building Materials Company
Analyzed operations and cost structure of this startup manufacturer projected to grow to over $80MM in sales in 5 years. Reviewed manufacturing equipment and operations, built a bottom-up cost model for current and future costs, and established requirements for scaling up the operations. The operational due diligence revealed necessary improvements to meet the very aggressive growth forecasts, as well as opportunities for cost reduction. PE client deferred investment.
Show Details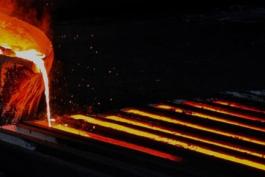
Properly Valuing Diverse Manufacturing Operations at Fabricated Metal Products Holding Company
Analyzed operations and cost structure of 5 independent companies engaged in forging, casting, and stamping operations. Deciphered cost structure, reviewed manufacturing operations, and analyzed material spend. Identified $7-15MM of labor, overhead, and material cost reduction opportunities in the largest of the companies, which was engaged in steel casting. Identified another $6-9MM in scheduling, labor, efficiency, and consolidation opportunities for the remaining companies. After delayed acquisition, now helping to capture opportunities.
Show Details
Operational Basics, Waste Reduction, and Productivity Improvements to Turn Around Declining Performance at Stationary Products Manufacturer
Identified $2+MM in opportunity from focusing on operational basics, e.g., measurement & reporting, material and labor procedures, and production scheduling. Implemented a paper waste measurement system to identify major sources of loss and then addressed root cause issues (e.g., setup waste, end-of-roll waste, material handling waste, and in-process waste). Within 6 months, material waste more than halved (from the original 40%+ levels) and labor productivity went up 15%.
Show Details