KPIs/ Measurement & Tracking

Implementing Measurement/Tracking/Reporting To Build Cost Discipline And Capture Material And Labor Cost Savings at Specialty Baked Goods Company
Identified $1.1-1.6MM in cost reduction opportunities in materials, labor, and freight. Launched a fact-based cost-reduction program including ingredient measurement and feedback system, a system for fixed labor standards based on rated line speeds, goal boards to manage productivity targets/performance, and a performance measurement and reporting system.
Show Details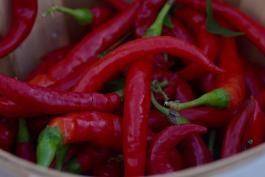
Performance Tracking Tools to Help New Management Make Fact-based Decisions at Leading Frozen Mexican Food Manufacturer
Constructed methodology and models to view profitability by customer, product, and channel. Results led new management to refocus product development/growth strategy on profitable products. Management succeeded in doubling revenue of profitable products and private equity owners sold firm to a strategic buyer in 3 years for a 26% compound annual return on investment.
Show Details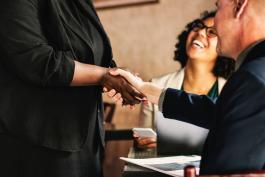
Dissecting Job Profitability and Redesigning Commission Structure to Improve EBITDA Margins at Professional Staffing Company
Conducted a 4-week operations assessment to establish levers to turn around the company’s EBITDA margin performance: 1) dissected the company’s cost and job performance, by cleaning/reconciling raw data from disjointed staffing and ERP software systems, mapping detailed general ledger costs to jobs, and creating job profitability profiles; 2) redesigned sales and recruiting commission structure for a 25% improvement in EBITDA; and 3) developed robust KPI-based reports required for managing cost and profitability moving forward.
Show Details
Rolling Out Waste Reductions and Productivity Best Practices at Specialty Printing Company
Identified $6-$12MM in purchasing, scheduling, and manufacturing savings opportunities (over 15% of total cost). Implemented client improvement team processes, developed standard operating procedures (SOPs), and implemented shop floor tracking and measurement systems.
Show Details
Redesigning Product Development Process to Increase Competitiveness at Tier 1 Automotive Interior Supplier
Developed a product development strategy that enabling affordable business structure and increase competitiveness. Created a balanced set of in-process, predictive performance metrics and a design structure matrix which enabled the development process to handle changes more efficiently and to minimize iteration loops. Project resulted in a proactive, cost- effective ability to ensure high quality product, reduced resource requirements, and an affordable, more competitive product development cost structure.
Show Details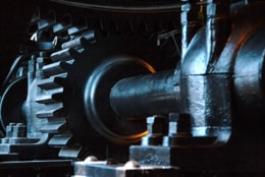
Determining the Right Fixed Cost Structure and Capturing Overhead and G&A Opportunities at Global Industrial Goods Manufacturer
Worked with senior business unit management to develop and implement manufacturing overhead and G&A savings recommendations across NA network. Established a zero-based organizational structure and cross-business unit management efficiency metrics for assessment purposes. First-year run-rate savings were $8.1MM, an additional $2.1MM of savings were targeted.
Show Details