Standardized/ Modular Product Design
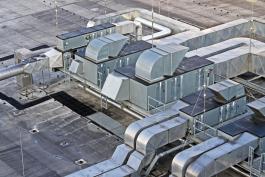
Establishing Operation End-vision for a Fast-growing, Entrepreneurial Climate Control Product Manufacturer
Conducted a 3-week operations diagnostic to establish an end-vision for optimizing the clients’s manufacturing, supply chain, and engineering operations. Gotham developed a solid fact base of the client’s operations, including demand patterns, inventory, labor efficiency, product complexity, and cost structure. Working with management, Gotham created an end-vision to transform operations and generate both real bottom line benefits – 600bp EBITDA improvement, 20-30% reduction in inventory, and 30% reduction in the plant footprint – and capability enhancements (faster speed to market, improved quality, etc.) that will allow the client to capture market opportunities and drive future growth. The company’s board wholeheartedly backed this end-vision and asked Gotham to help accelerate capture of these opportunities.
Show Details
Creating a Fact-based, Realistic Strategy for Performance Enhancement at Leading Industrial Machinery Manufacturer
Conducted a 2-week diagnostic of current performance as a first step in helping craft and execute an operations strategy. Specific elements of the proposed strategy included: (1) outsourcing non-core activities; (2) rationalizing the vendor based and developing focused supplier partnerships; (3) segmenting operations (equipment vs. consumables) to improve supply chain management; and (4) Moving towards standard and modular system design to greatly simplify inventory and production. Short-term cost savings of $2MM successfully captures and $3+MM longer-term savings capture on track.
Show Details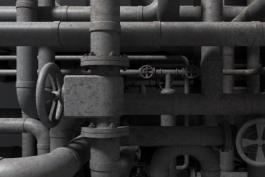
Assessing Product Design and Network Simplification Opportunities at Global Environmental Machinery Manufacturer
Analyzed product portfolio and design platforms, manufacturing and engineering facilities, and cost structure to establish cost reduction opportunities at a machinery manufacturer with operations distributed over 13 facilities in 8 countries. Due diligence identified $23-39MM (12-21% of total COGS) in cost savings from standardizing/modularizing product line and executing a low-cost manufacturing strategy, simplifying/consolidating the manufacturing and engineering network, and reducing material, labor, and freight costs.
Show Details
Improving UK Supply Chain Performance for Multi-National Soup Company
Worked hand in hand with UK manufacturing division managers to reduce and manage complexity, leverage purchasing scale, and simplify products, with a near-term target of capturing $5MM in aggregate savings in the first year while ensuring core operational processes were strengthened so that in year 2, the division could capture additional value from broader optimization of the supply chain. After 1 year, $4MM+ had been saved with another $2-3MM in savings expected over the next 6 months, and customer service had improved. Our team was then asked to review the entire European supply chain.
Show Details