Distribution & Logistics

Improving Cost-to-serve at Premium Baked Goods Company
Created a new logistics strategy, including implementing a new DSD network and delivery process, developing a new transportation and warehousing strategy, and re-balancing production among plants. Over 75% of the $2.5MM in savings (from a cost base of $12MM) highlighted in the strategy was saved in the first year of implementation.
Show Details
Cleaning Up Distribution as a First Step in Establishing a Growth-supporting Distribution Platform at National Seafood Company
Conducted a diagnostic to reduce distribution costs as a part of an effort to integrate the distribution systems of two companies by identifying and sizing cost levers with savings benefits (quick hits, process changes, and cultural changes). Targeted cost savings of $1.5 to 2MM on a base of $7MM, of which $1MM are estimated to be achieved by quick hits alone.
Show Details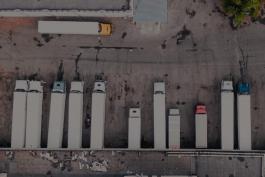
Unlocking Truck and Parcel Freight Savings at Portfolio Companies of Middle-market Private Equity Firm Freight
Created fact base for leveraging $11MM of freight spend across 3 portfolio companies of a middle-market private equity firm. Facilitated communication between management of portfolio companies to understand service requirements and the manner in which the individual portfolio companies would conduct freight negotiations. Led RFP process and analyzed new bids based on 2 years of historical freight spend. Created an evaluation matrix based on both cost and service to facilitate vendor selection. Purchasing consolidation led to $1.2MM in savings in the first year and improved freight service.
Show Details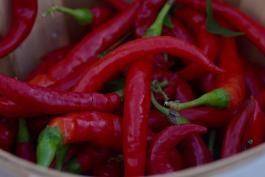
Performance Tracking Tools to Help New Management Make Fact-based Decisions at Leading Frozen Mexican Food Manufacturer
Constructed methodology and models to view profitability by customer, product, and channel. Results led new management to refocus product development/growth strategy on profitable products. Management succeeded in doubling revenue of profitable products and private equity owners sold firm to a strategic buyer in 3 years for a 26% compound annual return on investment.
Show Details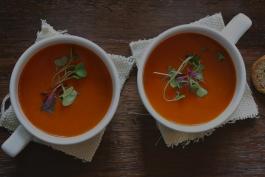
Refocusing North American Supply Chain for a New Competitive Environment at Global Soup Manufacturer
Created a North American Supply Chain strategy for a multinational soup company which had lost its scale advantages. Built upon a solid understanding of the company's operating strengths, the strategy leveraged collaborative alliances up and down the supply chain to extend the company's control of cans from fabrication to retail, and reduce costs in the entire system by 10-15%.
Show Details
Establishing Current and Potential Operations Value of Startup Fresh Soup Company Acquisition for National Fresh Foods Company
Performed operational due diligence for the acquisition of a fresh soup manufacturer that led to no-go decision as original cost savings estimate proved overly optimistic and investment requirement estimates proved too low. Identified stand-alone cost savings, constructed a catastrophe and failure scenario analysis, created a capital expenditure timeline in light of growth requirements and need to adapt process to manufacture U.S. style soups, and established forward COGS by identifying cutoffs for purchasing scale cost reductions and modeling labor requirements against growth targets. Assessed potential synergies, including soup revenue growth through shelf proximity and co-marketing with produce products, reduced soup logistics costs through use of existing produce cold-chain, lower soup raw materials cost through use of current suppliers and scale, and elimination of redundant overhead and SG&A expense through organizational consolidation.
Show Details